Capital-Executive Ship Management Participates in Major Project to Convert Offshore Vessel to Run on Ammonia-Powered Fuel Cell
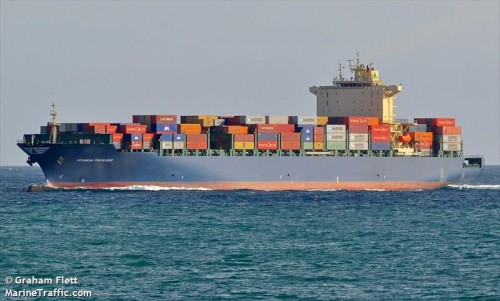
ShipFC consortium project gets €10m fund injection to deliver world’s first high-power fuel-cell to be powered by green ammonia.
A maritime innovation project looking to install the world’s first ammonia-powered fuel cell on a vessel has been awarded €10m funding from the European Union.
Athens, Greece, January 23, 2020. Capital-Executive Ship Management participates in the ShipFC project which is being run by a consortium of 14 European companies and institutions, co-ordinated by the Norwegian cluster organisation NCE Maritime CleanTech, and has been awarded backing from the EU’s Research and Innovation programme Horizon 2020 under its Fuel Cells and Hydrogen Joint Undertaking.
The project will see an offshore vessel, Viking Energy, which is owned and operated by Eidesvik and on contract to energy major Equinor, have a large 2MW ammonia fuel cell retrofitted, allowing it to sail solely on the clean fuel for up to 3,000 hours annually. As such the project will demonstrate that long-range zero-emission voyages with high power on larger ships is possible.
The goal is also to ensure that a large fuel cell can deliver total electric power to shipboards systems safely and effectively. This is the first time an ammonia-powered fuel-cell will be installed on a vessel. A significant part of the project will be the scale up of a 100-kilowatt fuel cell to 2 megawatts. The fuel cell is tested on land in a parallel project and development and construction will be undertaken by Prototech. Testing will be executed at the Sustainable Energy Norwegian Catapult Centre. The ship-side ammonia system will be supplied by Wärtsilä.
The ammonia fuel cell system will be installed in Viking Energy in late 2023.
Enhancing collaboration
The project represents the latest stage in the long running collaboration between Equinor, Eidesvik and Wärtsilä. The three companies successfully collaborated on a number of environmental and cleantech projects over the years. Viking Energy was the first LNG powered ocean going vessel in 2003, and Eidesvik and Wärtsilä also collaborated on the 2009-built Viking Lady, another LNG-fueled vessel that was seen as a milestone in the transition of shipping with its installation of fuel cells and marine batteries.
Capital Executive Ship Management Technical Director George Livanos said: “We are proud to contribute knowhow to this seminal project addressing current environmental and commercial challenges in the shipping industry”.
Eidesvik President & Chief Executive Jan Fredrik Meling said: “This is a result of hard work over time as we have continued to collaborate with Equinor on transformative projects. We are proud to be pioneers when it comes to introducing new energy carriers and fuels into the industry. This project to install the world’s first ammonia-powered fuel cell will help us continue our journey towards a decarbonized future and help maintain our competitive role”.
As an energy major and charterer of offshore vessels, energy group Equinor has set itself a high standard when it comes to investing in the future. “We see projects such as the ShipFC conversion to use ammonia on a high-powered marine fuel cell as an important step in finding the right sustainable and clean solutions in the future. Our ongoing collaboration with Eidesvik is testament to a long- standing belief that we can achieve our goals by working constructively towards that vision,” says Senior Vice President for Joint Operations Support in Equinor, Cecilie Rønning.
Norwegian crop nutrition company Yara has been contracted to supply the green ammonia which will be produced by electrolysis and delivered to Viking Energy containerised to enable easy and safe refuelling.
Another part of the ShipFC project will perform studies on three other vessel types, namely offshore construction vessels and two cargo vessel types, to illustrate the ability to transfer this technology to other segments of the shipping industry.
NCE Maritime Cleantech cluster chief executive Hege Økland says that this project represents another step in the right direction as shipping seeks ways to utilise new technologies and fuels to decarbonise. “Shipping has agreed to the goal of decarbonising by the end of the century and to have achieved a global 50% cut by 2050 based on 2008 levels. As we move onto the right trajectory to achieve these targets, we see interest in new fuels such as ammonia and hydrogen increasing. Ammonia is an abundant energy source and can easily be made from renewable resources making it one of the fuels that will likely meet part of shipping’s future energy demand.”
About Capital-Executive Ship Management Corp.
Capital-Executive Ship Management Corp. ('Capital-Executive') currently operates a fleet of 22 vessels including 4 modern bulk carriers and 18 container carriers with a total dwt of 1,926,712 tons approx. The fleet under management includes vessels of Nasdaq-listed Capital Product Partners L.P.
About the consortium members
Alongside NCE Maritime Cleantech (NO), Eidesvik Shipping (NO), Equinor (NO), Prototech (NO) and Yara (NO) in the European consortium are Wärtsilä Norway (NO) which will work on the fuel systems, any changes to the ship’s design and stability and the energy management of the vessel. Fraunhofer IMM(GE), an institute of the leading German organisation for applied research, has expertise with fuel cell process development and will assist Prototech in the development and construction of the ammonia fuel cell system. A specialised SME Persee (FR) is an expert in energy management controls and data.
The University of Strathclyde (UK) and National Centre for Scientific Research Demokritis (GR) are consortium members assessing any safety criteria.
The three test cases that will look at the ability to transfer the technology to other vessels has led to North Sea Shipping (NO), Capital-Executive Ship Management (GR) and Star Bulk Ship Management (CY) also being part of the consortium. One of the five Catapult centres in Norway, Sustainable Energy Norwegian Catapult Centre, has responsibility for testing autonomous sustainable energy systems as well as scale-up of the ammonia fuel cell.
Media contacts for more information:
Hege Økland
CEO, NCE Maritime CleanTech
Tel.: +47 957 53 695
Jan Fredrik Meling
CEO, Eidesvik
Tel.: +47 916 75 119
JanFredrik.Meling@eidesvik.no
Ingve Sørfonn
Head of Technology and development, Marine Electrical Systems, Wärtsilä
Tel.: +47 957 32 581
Bernt Skeie
CEO, Prototech
Tel.: +47 950 46 031
bernt.skeie@prototech.no
ShipFC project website: https://shipfc.eu/
ShipFC - Ammonia in shipping: Questions & Answers
Why ammonia as a fuel for offshore vessels?
Using conventional fossil fuels and means of energy saving alone will not enable the maritime industry to fully eliminate harmful emissions which is the ultimate goal set up by IMO regarding GHG emissions. Therefore, alternatives for energy storage will have to be investigated.
Ammonia is considered a balanced solution in terms of volumetric energy density and renewable synthetic production cost compared to other renewable fuels.
The advantages of ammonia?
- Ammonia can be a zero-emission fuel
- There are established infrastructure and safety protocols for the production, transport and storage of ammonia.
- Ammonia is also relatively well-suited for deep-sea applications, as the energy density of the fuel is high compared with many of the alternatives
What are the emissions from use of ammonia in the ShipFC-project?
We get no harmful emissions when using ammonia fuel in the ShipFC project. The ammonia fuel and oxygen air are electrochemically converted to nitrogen and water in a fuel cell while producing electrical power and heat. When using fuel cells, as opposed to a combustion engine, we stay well below the temperature limit for NOx formation.
How is ammonia stored?
Ammonia can be stored in liquid state at about minus 33 degrees Celsius under atmospheric pressures or at ten bars in room temperature. Ammonia is easier to store on the ship than hydrogen and it also has a more suitable distribution infrastructure in place as ammonia is already distributed on a very large scale on tankers carrying liquefied gases. Typically, the rules and guide lines for the carriage of ammonia is identical as LPG with some exceptions related to material selection and gas detection.
Is ammonia used in the project emission free?
When ammonia is produced with power from sustainable sources, it is CO2 neutral.
How is the ammonia in the ShipFC project produced?
The ammonia in this project will be produced by Yara from renewable sources (desalinated water, air, renewable electricity), using proven technologies (electrolyser, nitrogen production, Haber-Bosch process). This would result in a carbon-neutral fuel since the tank-to-propeller phase does not emit any carbon.
Isn’t ammonia toxic?
The handling of ammonia implies risks in the same amount as for other types of fuels. Ammonia is not as flammable as for example gasoline however it is highly toxic with potential adverse health effects. The project participants’ extensive knowledge within storage solutions, ship design and safety systems will keep risks related to the use of ammonia to a minimum.
The risk of ammonia and how to handle it?
The main risks of ammonia are the toxicity and environmental impact. Ammonia is a gas at atmospheric conditions and highly toxic. Therefore, with storing and handling ammonia adequate means are required to limit the likelihood and effect of exposure to humans and the environment. Considering the toxicity as ammonia can be lethal to humans at 2,700 ppm when exposed for a duration of 10 minutes, whereas ammonia can be smelled at 5ppm already, and 8 hours exposure limit is on 25ppm, which already would feel uncomfortable.
Ammonia is also a flammable gas though it is relatively hard to ignite compared to conventional fuels. The lower flammability limit of ammonia is 15% which is equal to 150,000 ppm. Therefore, the flammability risks of ammonia are relatively low compared to the toxicity risks. The ship design will learn from the safe design of ammonia plants, with respect to material choice, safety systems and emergency procedures.
Which safety precautions will be done?
The fertilizer industry has more than 100 years of experience working with ammonia. There are well established regulations in the industry that have been set up over the years. The knowledge and experience of the people working in this sector and the maritime sector, will be used as basis for developing a safe design of the ammonia FC system.
Why is ammonia chosen over hydrogen for this vessel?
Safety and regulatory challenges as well as space/ weight and cost considerations related to storing large quantities of H2 on ships have generated interest in exploring alternative hydrogen-based energy carriers. Several studies have pointed to ammonia (NH3) as a potential fuel for shipping .
There is also existing infrastructure for transporting and handling NH3 because large quantities of it are used as agricultural fertilizer.
Why using fuel cells and not directly use the fuel in the combustion engine?
Ammonia was used in internal combustion engines as early as 1933 but reformed to Hydrogen before sent to an engine. Liquid ammonia as direct fuel in an engine was done as early as 1943 in busses in Belgium. Korean researcher successfully tested a dual fuel car in 2016 running on 70% ammonia and 30% gasoline.
Typically, we expect that a certain amount of pilot fuel would be needed in an engine running on the Diesel principle, but this applies also for LNG when burnt in a diesel engine.
Internal combustion engines running on ammonia will be developed and several players on the marine industry (including Wärtsilä) has announced that ammonia is part of their fuel for the future on ICEs.
What kind of fuel cells will you use?
The project will use solid-oxide fuel cells (SOFC) thatoperate at temperatures in the range of 500-1000°C, at high efficiency. SOFC technology is used mainly in land-based power plants with electrical capacities up to 10 MW, and as residential combined heat and power systems using natural gas fuel. The ShipFC will use compact SOFC systems specifically developed for maritime use.
What is the cost of ammonia compared to MDO?
The business case for ammonia as a ship’s fuel will have to be supported by regulatory and economic factors in order to progress further. Today there is no scenario under which the zero-emission vessel options are likely to be more profitable than the MDO vessel. This underlines the importance of policy and regulation as drivers for change, since market forces alone appear unlikely to prove sufficient.
Where will the ammonia be produced?
Today, Yara produces ammonia at their facility at Herøya, Porsgrunn, Norway. Yara started the expansion of its fertiliser complex in January 2015 and it covers an area of approximately 1.5 km2. Yara is currently building their first pilot plant for green ammonia in Norway with a second large plant soon being built in Australia.
How will the bunkering of the ammonia take place (land-side and ship-side)?
Yara will supply certified green ammonia directly to the ship, combining ship-to-ship an rail-to-shop infrastructure. On the ship-side, it will be equipped with a large fuel tank what will provide enough fuel for on week in operation between bunkering.
Is green ammonia available worldwide on a commercial basis? When can it be available for shipping?
Currently 180 million tonnes of ammonia are being produced world wide (mainly natural gas based Steam methane reforming hydrogen production), of which most is (captive) used in fertilizer production. 20 million tonnes are being traded, of which Yara trades 25%. Green ammonia is under development, with the aim to have the first volume sin the market by 2022-23 (Yara Porsgrunn, Yara Pilbara)
Will additional energy systems/solutions be a part of the pilot?
Viking Energy has a large battery storage system that will be integrated with the fuel cell system to handle load levelling, but this system will not be charged to the project since it is already paid for.
How and when will the pilot period be conducted?
Viking Energy will pilot the FC system during a 12-month period starting December 2023, where the ship is operated for at least 3000 hours annualy with ammonia. The ship will most likely continue on its present operational profile – typically 3 roundtrips a week between the Mongstad offshore base north of Bergen and the Tampen area in the North Sea. Bunkering will be carried out at the offshore base, and the Ammonia tank system will be designed for bunkering of Ammonia at least once a week, designed to support Viking Energy’s operational profile. After the possibly successful pilot phase, we aim for the system to be used for continued operation of Viking Energy running on Ammonia for up to 90% of the time.
Why are three other ship owners besides from Eidesvik involved in the project?
In addition to Eidesvik’s Viking Energy, three other ship owners are involved in the project as replicators. These ship replicators will do feasibility studies on applying FC technology and a wider ammonia distribution infrastructure on their operations. The result will be an evaluation of the possibility to use ammonia fuel cells in use cases with larger vessels from other segments as cargo and bulk. This means use cases with 20MW+ systems that has higher power demand than Viking Energy. The objective of the replicators is to prove that the technology is scalable to other ship segments.
What is ammonia?
NH3
Colourless pungent gas
Used in /as:
– Fertilizer industry
– Pharmaceuticals
– Cleaning products
– Refrigerant
Made today predominately from fossil fuels
The last Green ammonia plant in Norway was closed down in 1993 (Glomfjord), hence Green Ammonia is not a new invention but more reinventing it.